Plasma activation for surface activation and modification
If surfaces have to be varnished, printed or glued, they require good wettability of the surface for good adhesion. Many surfaces show insufficient wettability even in a clean state, which is intensified by impurities. As a result, liquids like adhesives and inks roll off. This is because the surface tension is very low and insufficient for further processing. If unprocessed material is processed, the result is often that paint and varnish do not adhere properly and quickly come loose again or that bonded parts fall apart. This can be prevented with plasma activation and surface modification.
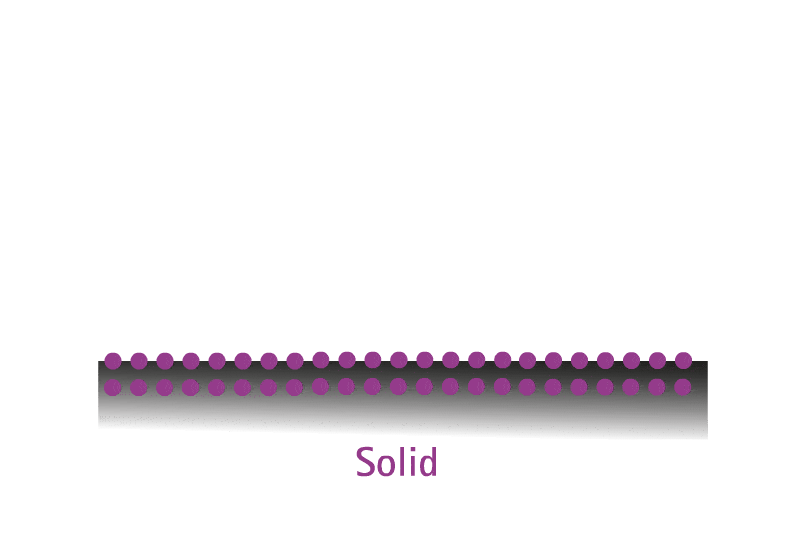
Plasma activation of a surface increases its surface energy and creates molecular anchor groups that correlate with those of the liquid. This manifests itself through improved wetting and leads to an optimized adhesion of suitable liquids.
Practical example: Plasma activation of polyphenylene sulfide
In the example, two polyphenylene sulfide components were treated with atmospheric pressure plasma from the plasmabrush PB3 system.
Suitable materials
The following materials can be plasma activated:
Plastics
Metals
Anorganic Materials
Furthermore, plasma treatment of natural leather, artificial leather, natural fibre, wood or paper is also possible.
Advantages of plasma activation
- High process speed and reliability
- No running costs
- Environmentally friendly treatment without additional chemicals
- Easy inline integration and automation
Technical articles on the topic
To make it easier for a system developer to work with MediPlas, relyon plasma provides the MediPlas evaluation kit. This kit is primarily intended for research laboratories, standardization institutes, material testing laboratories, didactics/training, PAW manufacturers and many others. With this plug-and-play board, a plasma can be created to generate gases with a variable composition of reactive oxygen and nitrogen species (RONS).
Before bonding: how long does a plasma treatment last?
How long does a plasma treatment last? This depends heavily on the material, the plasma device used and other influencing factors.
Plasma technology live at the MD&M trade fair
relyon plasma will showcase innovative solutions for disinfection, adhesion optimization, and the integration of plasma technology into industrial processes at the MD&M fair in Anaheim (USA) from February 4 to 6, 2025. Visitors can look forward to exciting live demonstrations on-site.
43. ak-adp workshop in Leipzig
From April 26-27, 2023, relyon plasma will present the piezobrush® PZ3-i at the 43. ak-adp workshop in Leipzig as part of the #ZukunftADP 2021.
Grounding of conductive substrates
When using PAA® technology, the ignited plasma bridge can be used for electrical grounding of conductive substrates.