Our innovative plasma technology
The term plasma is increasingly used today because plasma technology has already established itself as a key and cross-sectional technology in many industries as a modern technology standard. But what is plasma?
What is plasma?
When it comes to plasma, we speak about the fourth aggregate state – besides solid, liquid and gaseous. By supplying so much energy to a gas that the critical number of electrons leave the atomic shell, the gas is ionized and moves from a gaseous state to a fourth state – plasma is formed. Energy is usually supplied by the application of a high-voltage source. The plasma that is generated is a matter with a high, unstable energy level.
Although physicists and chemists only started talking about plasma in relatively recent times, plasma related phenomena have played a role in the life of human beings ever since primeval times. Lightening created fire and the northern lights made our forefathers contemplate the existence of higher beings. Both of these natural effects are based on plasmatic discharges.
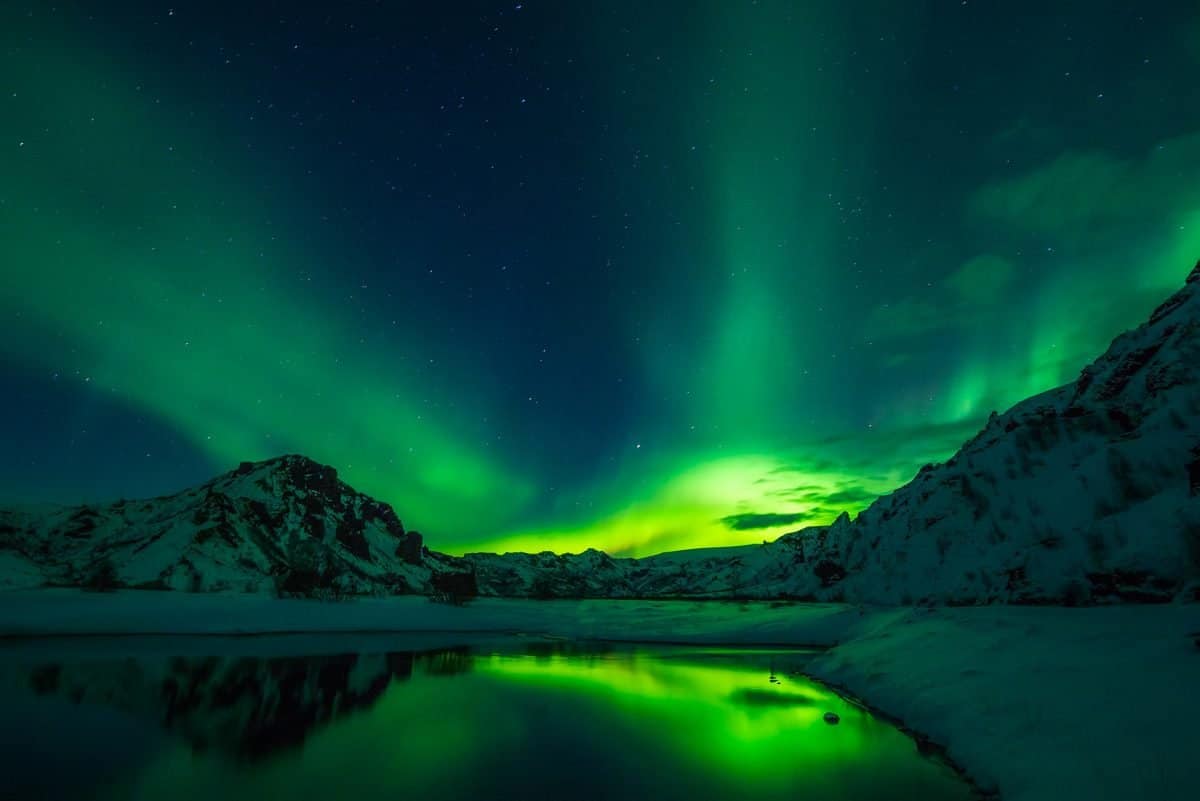

The history of experimental plasma physics began around the year 1700 with attempts to create electrical luminous effects in evacuated glass bulbs. In 1747 Benjamin Franklin invented the lightening conductor and Michael Faraday first raised the question of the four states of matter: solid, liquid, gas and fire as the fourth state (plasma). Werner von Siemens developed the first technical plasma application in 1857 with his ozone generator, which was used to generate ozone by means of electrical discharge.
Ground-breaking developments in lighting technology (neon tubes, glass lasers, plasma displays), and in plasma chemistry, for example, in the production of diamond coatings or plasma welding, are based on the ability to master the fourth state of matter and have become an integral part of everyday production. Today, plasma technology is in the process of fundamentally revolutionising conventional production procedures in industry, as well as applications in the hygiene sector and in medical technology.
Here at relyon plasma we have decades of experience in the development and implementation of specialist and innovative plasma components for manual and in-line processes.
Mode of action of atmospheric pressure plasma
Atmospheric pressure plasmas, produced by electric discharges in the air or other working gases, possess a unique combination of properties such as being chemically active, cold, and at the same time environmentally friendly, safe and cheap. Such plasmas produce large quantities of very reactive, but short-lived chemical species. These species can disinfect, clean, modify and functionalize a broad range of surfaces, preparing them for adhesive bonding, varnishing, and printing. Plasma pre-treatment dramatically improves the quality of the results.
While being very effective, the plasma is cold; it does not overheat the surface. The treatment extends only to an nm-width thin surface layer and it does not affect the surface visually. Moreover, the process does not use toxic chemicals, and the reactive chemical species, produced within the plasma, decay within milliseconds after the treatment. This makes the plasma treatment is safe and environmentally friendly.
Atmospheric plasma equipment is significantly cheaper compared to the low-pressure plasmas, as it does not require expensive vacuum chambers and pumps. Furthermore, in most cases it uses air as the working gas, cutting the need for expensive gases. At the same time, it is very versatile – it can be integrated into both, the batch and the running conveyor production lines. Thus, plasma increases production throughputs, while saving on chemical consumables, safety equipment, and training.
Upon contact with the treated surface, the chemically active cold atmospheric plasma initiates a multitude of physical and chemical processes. The main reaction agents are highly reactive short-lived neutral chemical species, which are produced by the plasma in large quantities. Additionally, when the electric discharge touches the treated surface, the latter is also irradiated by VUV light and bombarded by the energetic electrons and ions. Although the quantities of the charged particles are small, their highly reactive nature strongly enhances the effects of the plasma. The following processes contribute to the promotion of the adhesion by the plasma treatment:
- Plasma cleans the surface: Plasma breaks organic bonds of heavy organic molecules producing lighter and more volatile molecules evaporating from the surface. Further, reactive chemical species oxidize organic contaminants forming carbon oxides and water vapor. As the plasma breaks contaminants turning them into vapor, no residues are left on the surface, leaving the latter in the ultra-fine clean state.
- Plasma reduces metal oxides: Plasma discharges, ignited in the forming gas, which typically contains 5 % of hydrogen and 95 % of nitrogen, produce large quantities of reactive hydrogen species. By contact with oxidized metal surfaces, they react with metal oxides reducing them to metal atoms and water vapor.
- Plasma strengthens the surface: With the increased treatment strength, plasma removes nm-scale weak surface layers having the lowest molecular weight. The bonds of the polymers, broken by the plasma, cross-link forming a stronger surface layer.
- Plasma induces a phase transitions and polymer molecules scission: With a further increased treatment strength, plasma induces a phase transition from the crystalline to the amorphous structure of the surface layer. The latter diffuses easily into the glue, increasing the strength of the diffusion adhesion. Moreover, plasma breaks polymer molecules, exposing their scissed open ends on the treated surface. This further increases the diffusive bonding strength.
- Plasma deposits chemically functional groups and increases the surface wettability: By reacting with the polymer molecules, plasma species deposit polar OH and ON groups on the cleaned surface significantly increasing the energy of the surface and its wettability. As the results, the subsequently applied paint wets the surface efficiently and fills the microstructures due to the capillary action.
- Plasma microscopically roughens surface: Electric discharges having direct contact with the substrate, especially the electric arcs burning on the metal substrate, when the latter is used as a cathode, erode the substrate surface on the micrometer scale. This creates microstructures that are filled by the adhesives improving their mechanical binding to the substrate.
Applications
Different applications – different technologies
Dielectric Barrier Discharge (DBD Technology)
For environmentally friendly processes for odour elimination and germ reduction
Piezoelectric Direct Discharge Technology (PDD Technology®)
For sensitive processes requiring cold active plasma.
Pulsed Atmospheric Arc Technology (PAA Technology®)
For fast processes that require maximum performance.
Relyon plasma’s plasma products have already been successfully integrated into the following applications:
- Surface activation and functionalization to increase wettability
- Cleaning of metals, glass and plastics
- Preparation for coating processes
- Plasma-assisted adhesive joints and laminating processes
- Optimization of digital and 3D printing
- Improvement of seals
- Plasma-induced reduction of metal surfaces
- Food treatment for quality and longer shelf life
- Sterilization of tissue and surfaces heat-sensitive plastics
- Germ and odour reduction
According to the different demands that our customers have on us, we have two different technologies in our product portfolio:
Advantages of atmospheric pressure plasma technology
What is the advantage of atmospheric-pressure plasma over low-pressure plasma? Atmospheric plasma systems are much cheaper than low-pressure plasma systems because they do not require expensive vacuum chambers and pumps. In addition, in most cases compressed air is used as process gas, which reduces the need for expensive gases. At the same time it is very versatile – it can be integrated both into batches and into the running conveyor systems. Thus, atmospheric pressure plasma increases production throughput while saving chemical consumables, safety equipment and training.