MediPlas Reactor
High-performance RONS generator as a component for industrial and medical applications
The MediPlas Reactor is a high-performance RONS (reactive oxygen and nitrogen species) generator. Depending on the selected process parameters and the type of gas supplied, the following reactive species are formed in the reactor: Ozone, hydrogen peroxide as well as nitrogen oxides. The exact composition of the medium can be varied according to customer-specific requirements.
It is based on cold atmospheric plasma (KAP) and can be integrated into applications as a component for cleaning, sterilization and disinfection. It was developed for the food, beverage, and pharmaceutical industries. But the principle can also be used in medical technology. To learn more about MediPlas in medical applications click here.
We are looking for partners who would like to benefit from the advantages of our DBD components and integrate our modules into their systems.
We are looking for partners >>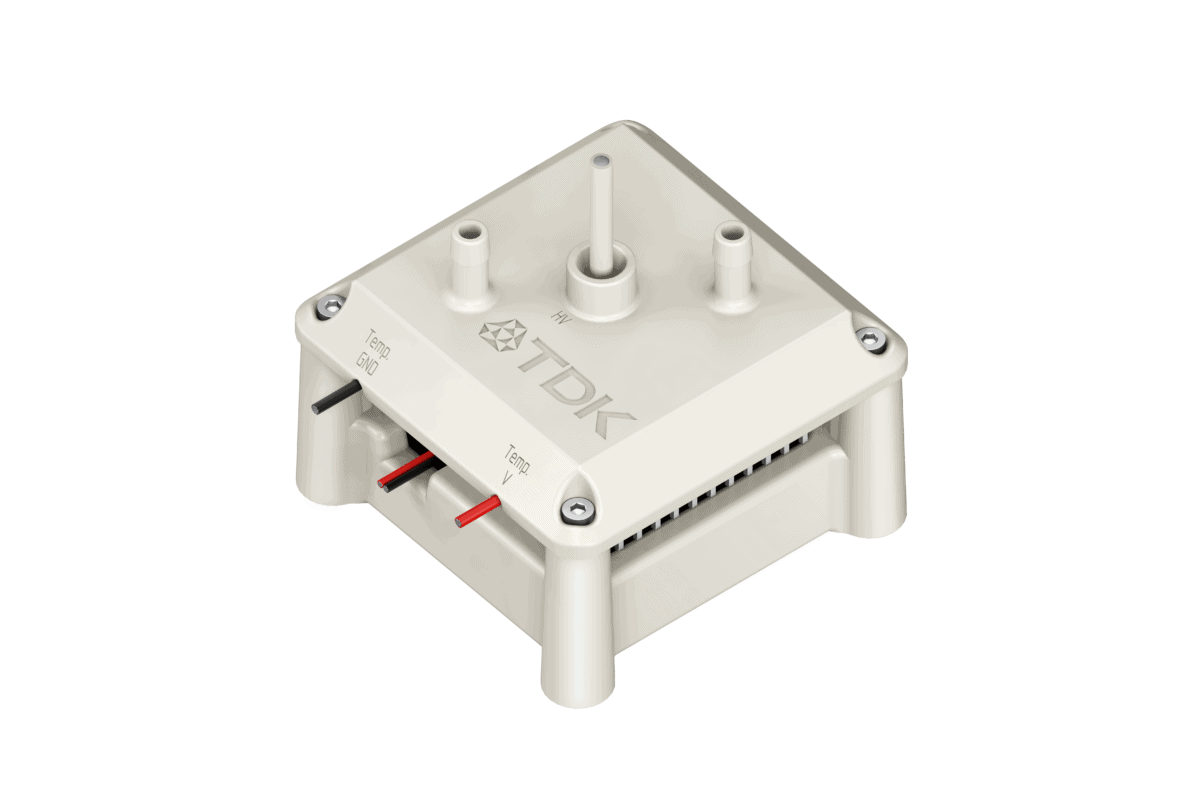
Applications of the ozone generator
- Pharmaceutical industry
- Packaging industry
- Food and beverage industry
- Agriculture industry
- Automotive industry
- Medical technology
- Dental sector
Application examples in video
The MediPlas RONS generator can be used in a wide variety of applications. In the video you can see the following experiments:
- Oxidative decolorization of organic dyes
- Ozone treatment of food against microorganisms
- Oxidative bleaching of textiles
- Cleaning of the inside of a hose
Use in Cleaning in Place
The cold atmospheric plasma components can be used wherever hygiene is an important consideration. This can be optimized by incorporating ozone into Cleaning in Place (CIP). Instead of the typical six steps, only four steps are required due to the incorporation of ozone.
Cleaning in place is a method for cleaning continuous processes without dismantling the system. The method was originally developed for the food, beverage and pharmaceutical industries. But the principle can also be used in medical technology.
Sterilisation in Place (SIP) is mainly used in pharmaceutical and biological production facilities and serves not only to clean but also to sterilise the system. Usually, sterilisation takes place through superheated steam or with special chemicals. The cleaning or sterilisation cycle can be optimised on site by integrating ozone into the process.
Application in the medical field
The MediPlas system can also be used for disinfection in medical technology. You can find further information on its use in the medical sector on the website of our parent company TDK Electronics: MediPlas landing page
Customised output gases of the gas flow reactor
The MediPlas system does not require additional chemicals or high temperatures, but uses only air (or oxygen) and electricity to produce efficient sterilizing gases.
Input gas → Output gas:
- Oxygen (O2)→ very high ozone concentration (O3)
- Dry air (O2 + N2) → Ozone; temperature-controlled Nitrogen oxides (NOx)
- Humid air (O2 + N2 + H2O) → Ozone; temperature-controlled Peroxides and acid
Technology
- High durability; easy integration
- High ozone concentration
- Stable against humidity
- Operates with pure (medical) oxygen to provide high ozone concentrations > 50,000 ppm. High oxygen concentrations can also be provided with pressure swing absorption (PSA).
- High NOx operation for inline fertilization for plants.
Versatile gas flow reactor products
Input → products:
- Oxygen → very high ozone concentration.
- Dry air → ozone; temperature controlled NOx.
- Humid air → ozone, temperature controlled Peroxides and acid
Technical data of the ozone generator
- Max. input power: 40 W
- W x H x L: 78 x 63 x 78 mm
- Weight: 230 g
- Max. concentration (when supplying dry air): 4.000 ppm O3
- Max. ozone quantity: 5 g/h
Advantages
- High efficiency
- High ozone concentration
- Compact size
- Easy integration into the unit
- Variable gas flow
- Durable
- Active temperature control
- Made in Germany
Advantages of the MediPlas system for end customers
- Low cost per cycle
- Avoidance of chemicals
- Short process time
- Environmentally friendly
- No use of consumables
More information on the MediPlas Reactor can also be found at our parent company TDK Electronics.
More information >>Downloads
Beschreibung/Description | Sprache/Language | Download |
---|---|---|
Flyer MediPlas | EN | Flyer |
Flyer MediPlas | DE | Flyer |
Data sheet MediPlas Reactor | EN | Data sheet |
Data sheet MediPlas Driver | EN | Data sheet |