Surface treatment
For the processing and end use of materials, their surface properties are of enormous importance. These can be positively influenced by specific surface treatment with plasma to achieve a perfect end result. Thus, purity and wettability of the surface are of decisive importance for the optimization of adhesion during bonding, printing, painting or coating. The wettability of the surface depends on the surface tension of the carrier material.
Even in a clean state, many surfaces have insufficient wettability, which is further worsened by contamination. As a result, liquids such as adhesive or ink can drip off and not adhere. This is referred to as a state of low surface energy of the solid. If this surface energy is lower than the surface tension of the liquid, the wetting and thus the adhesion is insufficient. Plasma activation of a surface increases its surface energy and molecular anchor groups for the applied liquid are formed. This manifests itself through improved wetting and leads to optimized adhesion of suitable liquids.
After plasma activation, success can be measured using contact angle measurement and test inks.
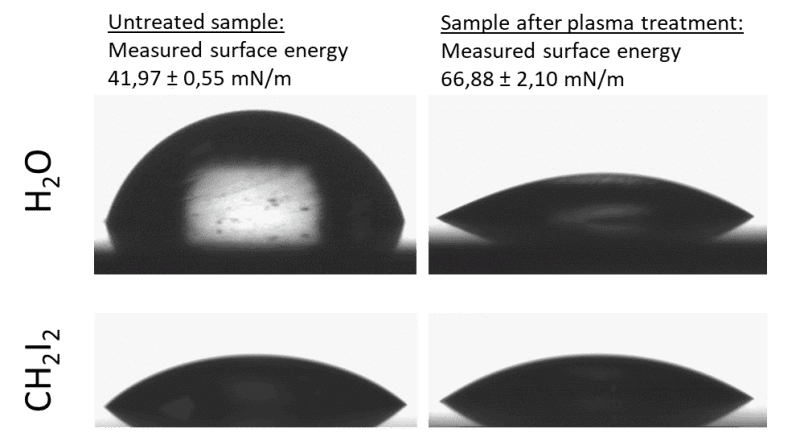
Fig. 4: Determination of the steel components surface energy before and after the plasma activation
Requirements for surfaces
Strong high quality adhesive bonding between dissimilar materials, such as paint and a plastic substrate can be formed by fulfilling the following requirements:
- Ultra-clean surface: The surface has to be free from contaminants. Even visually clean surfaces can contain contaminants such as adsorbed organics, water, monomers, release agents, oils. Ultra-fine clean state is difficult to achieve with conventional cleaning techniques which often leave residues.
- Oxide-free metal surface: The best adhesion to metal surfaces is achieved when they are free from metal oxides. However, in the air metals oxidize quickly. Thus, the time between the removal of the oxide layer and the application of the adhesive usually needs to me minimized down to milliseconds.
- Strong surface: In the case of plastic polymers, formed by molding and extrusion processes, the uppermost nm-width surface layer consists of low molecular weight and not cross-linked polymer molecules. This surface layer is mechanically weak. Removing this weak layer and cross-linking the polymer molecules in the remaining layers improves the adhesion strength.
- Wettable surface: For the adhesive to cover (wet) the surface efficiently, the surface energy of the adhesive should be lower than that of the surface they should be bonded to. However, mechanically strong adhesives and paints usually have high surface energy. This poses a serious problem for their use with most plastic polymers, which typically have very low surface energy.
- Amorphous surface with diffusion of polymers: Plastic polymers have a semi-crystalline structure with regions of either crystalline or amorphous materials. Diffusive bonding, achieved by glues, is stronger with the amorphous material, when the polymers are free to diffuse into the glue. Plasma treatment promotes the scission of polymer molecules present on the surface, which facilitates their diffusion and strengthens their bond with the glue.
- Chemically functional surface: On the molecular level, the adhesion between two materials is mediated by either electric attraction between the surface molecules and the molecules of the adhesive, or by their chemical bonds. The former type, called dispersive adhesion, is strong when polar molecules cover the surface. While surfaces of plastic polymers are typically non-polar, formation of the layer of polar molecules functionalizes the surface. This is sufficient for more printing applications. The latter type, called chemical adhesion, forms the strongest joints. However, chemical bonding between dissimilar materials in not possible. An intermediate layer of molecules having chemical affinity to both, the surface and the adhesive, functionalizes the surface enabling very strong chemical bonding.
- Microscopically rough surface: When the surface is well wettable by the adhesive, the latter can efficiently fill the surface pores and irregularities due to the capillary action. This increases the mechanical strength of the adhesive bonding.