Improved adhesion: Optimized adhesive bond with plasma
When plasma is used to functionalize a surface prior to bonding, the resulting optimized bonds will display a strong adhesion improvement. Plasma can be used on a wide variety of materials: metals, glass, ceramics, and even natural materials such as woods and textiles respond very well to plasma functionalization. For several our customers, it is especially important that many polymers with typically “non-stick” surfaces can be successfully glued and bonded following plasma treatment.
This surface functionalization achieved by plasma processing relies on a combination of effects: ultra-fine surface cleaning from organic contaminants, modification of the surface topography, modification of the crystalline structure of the surface layer, and deposition of functional chemical groups. Metals can be cleaned of hard oxides, restoring the sheer metal surface.
The atmospheric pressure of our plasma systems is generated using air or typical industrial gases such as hydrogen, nitrogen or oxygen. For our customers, this means a huge improvement regarding cost-efficiency, process safety and environmental compatibility, as expensive vacuuming equipment or wet chemistry are simply no longer necessary. Fast processing speeds make our system suitable for a wide variety of industrial applications.
The table shows a comparison of the pull off strength of bonding untreated plastics and the same plastics with previous plasma treatment with 2K epoxy adhesive. The comparison shows a significant improved bonding:
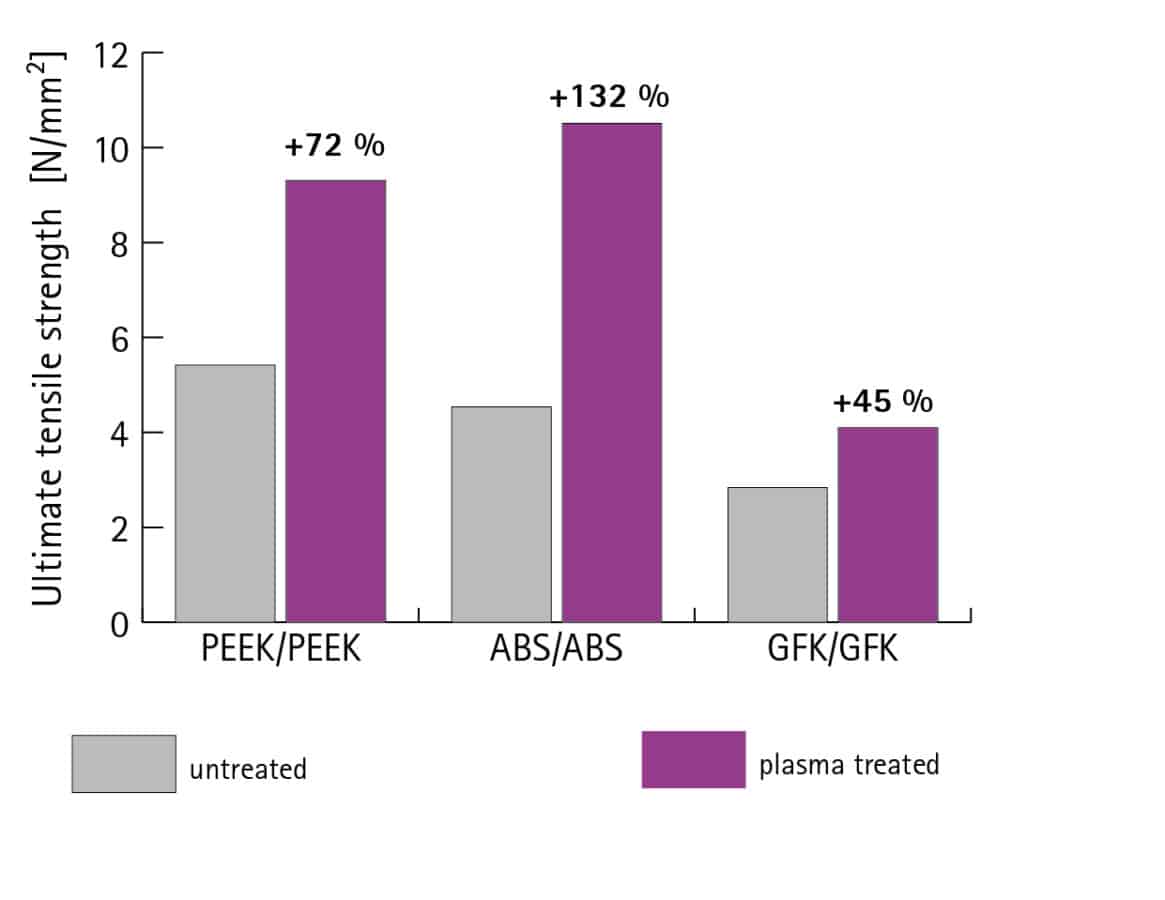
Advantages of plasma processing before bonding
Plasma cleans, strengthens and chemically functionalizes the surface. All these effects, which are required for adhesion improvement for bonding processes, are achieved simultaneously in a single step:
- Ultra-fine cleaning, no residues
- Gentle, non-destructive surface treatment
- No wet chemistry
- Air or cheap non-toxic working gases
- Environmental friendliness
- No expensive vacuum equipment
- Fast processing speeds
- Easy integration into existing production lines
Application examples
Better bonding with atmospheric pressure plasma
Prof. Dr. Bender examines the interaction of surface roughness and surface energy with polyethylene and how better bonding with atmospheric pressure plasma can be achieved.
Customer reference: Space Team Aachen
The piezobrush PZ3 can be used efficiently in rocket development. Space Team Aachen uses it for the pre-treatment of carbon fibre reinforced plastic and aluminium interfaces.
REGIOTAPE GmbH uses the piezobrush PZ3 for effective plasma pretreatment before bonding a wide variety of materials.
Influence of plasma on the shear bond strength of PAEKs to composite resin
The objective of this study was to investigate the influences of non-thermal plasma on the shear bond strength of PAEKs to composite resin.
A Novel Fabrication Process for Pneumatic Soft Actuators
Tinsley and Harris used computer-controlled localised plasma treatment with the piezobrush® PZ2-i to selectively modify the chemical behaviour of silicone and PET to produce pneumatic soft actuators.