Surface treatment with plasma technology for ideal processing
Professional article Galvanotechnik
Author: Richard Suchentrunk
https://www.leuze-verlag.de/fachzeitschriften/galvanotechnik
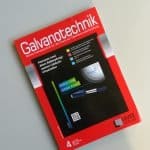
The company
Relyon plasma GmbH in Regensburg is a relatively young and innovative company in the field of plasma technology. Relyon plasma was founded in 2002 as a 100% subsidiary of the internationally renowned Maschinenfabrik Reinhausen, which was launched on the market under the name Reinhausen Plasma in 2004. In the course of a management buy-out, Reinhausen Plasma GmbH was renamed relyon plasma in 2014. In 2018, relyon plasma expanded its market presence with the new shareholder TDK subsidiary EPCOS AG. The aim of this alliance is to develop and market innovative cold-plasma technologies.
Thanks to many years of professional industry experience, relyon plasma now offers a wide range of specialized plasma components for manual applications and inline processes. Atmospheric pressure plasmas generated by electrical discharges in air or other gases have a remarkable combination of properties that make a unique surface treatment possible. Such plasmas produce large quantities of highly reactive but short-lived chemical species. They can disinfect, clean, modify and functionalize a wide range of surfaces and prepare them for bonding, painting and printing.
Plasma pretreatment significantly improves the quality of the results. In addition, Relyon Plasma’s plasma technology is used for sterilisation, tissue stimulation and odour neutralisation in laboratory and medical applications. As a modern, technology-oriented company with a slim structure, the Regensburg-based company realises reliable plasma solutions “Made in Germany”. Here the technologies for the products are developed with joy and innovation. Function, efficiency and reliability for satisfied customers is the decisive goal.
In addition to flexibly usable proprietary products, relyon plasma develops customer-specific OEM components up to series maturity in order to optimize surface properties rationally and environmentally friendly and to contribute to product and patient safety in the hygienic area. All OEM products developed by the company or by customers can be easily integrated into new or existing production and control systems and complement or modernize automation processes.
The technology and products
Two different technologies have been implemented in relyon plasma’s product portfolio according to the different requirements. The Piezoelectric Direct Discharge Technology (PDD technology) is used whenever sensitive processes require a cold active plasma. Pulsed Atmospheric Arc Technology (PAA technology), on the other hand, is used when highest performance and fast processes are required.
The advantages of the PDD technology® (Piezoelectric Direct Discharge) are obvious: Piezoelectric direct discharge is the most efficient excitation technology with maximum active plasma yield. The cold active plasma process is compatible with any material. The device lies ergonomically in the hand and is safely operated via a simple plug-in power supply. No external gas supply is required.
A particularly compact and long-term stable high-performance plasma generator in nozzle form is realized by the combination of a unipolar pulsed high voltage source and a vortex flow in the nozzle (PAA Pulsed Atmospheric Arc Technology®). In this dynamically controlled operating mode, the arc is prevented from stabilizing at a hot spot and nozzle erosion is minimized. The powerful atmospheric plasma system is unique in terms of power density and function. It can be easily integrated into any process environment, operates safely and reliably, and is optimized for industrial and high-speed applications. The proven plasma system Plasmabrush® PB3 is characterized by low weight and compact design of the plasma head. This allows the full dynamic range of motion to be exploited. The efficient PS2000 high-voltage source provides the power for all practical requirements.
The plasmacell P300 is a closed ideal processing cell for a clean environment, the operation is simple and intuitive. The included Teachbox makes programming the treatment sequence child’s play. In addition, all functions can be controlled by software via an optional touch screen. All work sequences and process parameters are displayed and stored. The system is delivered tested and fully installed, all options can be easily retrofitted. Thanks to its modularity, the basic system is consistently optimised for ergonomics and occupational safety.
The hand-held unit with highly efficient pulsed atmospheric plasma is ergonomically optimized for safe working in industrial environments. Thanks to the trolley construction, it can be used anywhere. The unit is powered by a single 230 V power source. An integrated air compressor supplies the plasma generator. It is easy to operate and guarantees maximum operating safety. The necessary two-hand operation and a signal lamp protect and warn the operator and third parties. Only a socket is required for commissioning.
Application examples
Wetted leather
Varnish removal
Reduction
You can download the original article here.