Plasma pre-treatment in car body construction
Introduction
Der PiezoBrush PZ3 wurde bei einem deutschen Sportwagenhersteller im Rahmen einer Versuchsreihe zur Effizienz verschiedener Oberflächenbehandlungen eingesetzt. Ziel war es, die Klebfähigkeit einer kontaminierten Oberfläche zu verbessern. Der PiezoBrush PZ3 wurde zur Plasmavorbehandlung im Karosseriebau aufgrund seiner handlichen Gestalt und des einfachen Einsatzes gewählt. Außerdem ist die kurze Aufrüstzeit des Verfahrens ein entscheidender Faktor. Dies ermöglicht akute, partikuläre Oberflächenaktivierungen auch in schlecht zugänglichen Stellen. Im Experiment wurden eloxierte und teils mit Schmierfett beölte Aluminiumprobekörper behandelt. Diese wurden anschließend verklebt und einem Zugscherversuch unterzogen.
Specimen production
During the test, various aluminum sheets were provided with different degrees of oiling. The test specimens were then treated using the PiezoBrush PZ3. The Nearfield module was used for this. The parameters were set to 100 % power with a 15-second timer. In an alternating movement, the 25 x 12.5 mm processing surface was treated for 15 seconds in staggered paths at right angles to the direction of loading. A distance of approx. 2 mm from the joining part was maintained as constantly as possible. The sheets were then glued together promptly. The dimensions of the test specimens corresponded to those of DIN 1465 and the adhesive thickness was 0.2 mm.
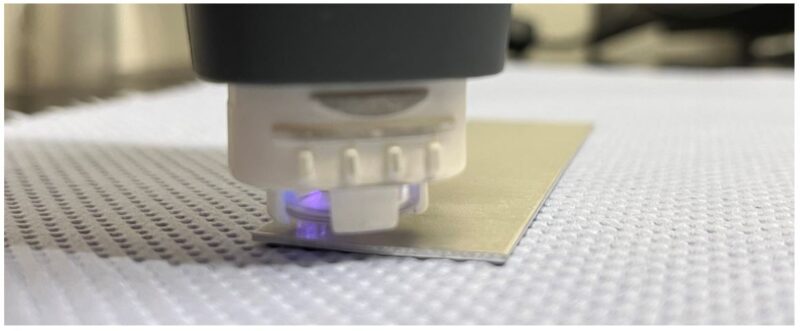
Results
The treatment method was validated using two procedures. On the one hand, test inks were used to verify surface activation before bonding and a contact angle measurement was carried out using distilled water. On the other hand, bonded test specimens were subjected to the tensile shear test. An epoxy adhesive was used as the adhesive.
For the test with the test inks, the test specimens were treated longitudinally on one half (left in the picture) and then the test inks were applied. These clearly show the increase in surface energy. Figure 2 shows the results with a surface tension of the test ink of 40 mN/m.
Furthermore, when treating heavily oiled surfaces, it was noticed that the high temperatures lead to changes in the grease on the surface. Figure 3 shows a slightly altered structure in the marked area. This suggests that heating the grease above its typical processing temperature causes the grease to resinify.
The evaluation of the tensile shear tests and contact angle measurements was carried out in comparison to an untreated surface with the same degree of oiling.
Diagram 1 shows the results of the contact angle measurement.
The plasma pre-treatment lowers the contact angle of the water droplet. This indicates improved surface activation. However, a regressive progression of the contact angle over time can also be seen. This is due to residual surface contamination. The impurities are dissolved in the water droplet and reduce its surface energy.
The results of the tensile shear tests are shown in Diagram 2.
The tensile shear strengths show that plasma pre-treatment increases the adhesive strength up to a degree of oiling of 1. The plasma process is capable of fine cleaning up to this degree of oiling and simultaneously activates the surface. At higher degrees of oiling, the contamination layer prevents surface activation, which is why there is no increase in tensile shear strength. Instead, the tensile shear strength is reduced. This could be due to the fact that the high temperatures of the plasma resinify the oil layer. As a result, the adhesive is less able to incorporate the impurities into its polymer lattice and therefore achieves lower strengths.
Summary
Die Plasmavorbehandlung mit dem PiezoBrush PZ3 im Karosseriebau besitzt großes Potential für die Klebvorbereitung gering verunreinigter Oberflächen. Durch die Aktivierung der Aluminiumoberfläche konnten die Zugscherfestigkeiten von 25,3 MPa auf 26,9 MPa erhöht werden. Vor allem aufgrund der handlichen Bauweise bei gleichzeitig guten Aktivierungseigenschaften der Oberfläche eignet sich der PiezoBrush PZ3 zur Klebvorbehandlung schwer erreichbarer Klebenähte. Die weitere Verwendung für die partielle Oberflächenvorbehandlung ausgewählter Bauteile soll in weiteren Schritten mit dem Fokus darauf, bei welchen teilen sich das Gerät mit wirtschaftlichen Vorteilen einsetzen lässt, evaluiert werden.