Surface energy
Determination of surface energy by means of test inks and contact angle measurement, enhancement through plasma treatment
Wettability is of major importance for all kinds of surface treatments like printing, varnishing and gluing. It describes the behaviour of liquids on solid surfaces which is dependent on the surface tension of the liquid and the surface energy of the solid. Both quantities are typically measured in Millijoule per square meter (mJ/m2), or Millinewton per meter (mN/m) or dyne per centimeter (dyn/cm). As an example, the surface energy of water at 25°C (77°F) is 72 mN/m. If a water droplet placed on a surface does not contract but forms a film, this surface has an energy of at least 72 mN/m.
Based on this principle, so-called test inks can be used as a quick method of estimating the surface energies of solids. Test inks of a wide range (usually 18 to 76 mN/m) can be purchased at arcotest GmbH:
arcotest GmbH
Rotweg 25
71297 Mönsheim
Germany
info@arcotest.info
www.arcotest.info
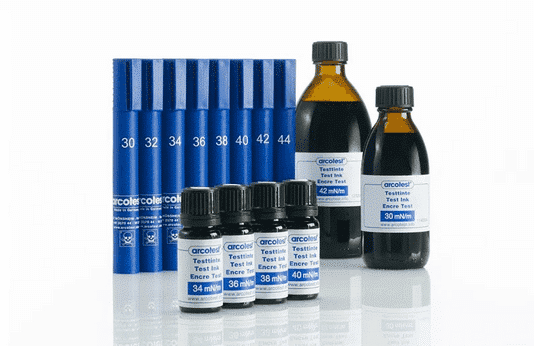
After applying the test ink of a certain value on a surface it is observed whether it contracts within a few seconds. If so, the surface energy of the substrate is lower than the test inks nominal value. In this case one would apply test inks with lower values until one of the test inks shows ideal wetting on the surface, i.e. does not contract within the first couple of seconds. The value of this test ink thus corresponds to the surface energy of the substrate.
A more accurate determination of the surface energy can be achieved by contact angle measurement. If the surface tension of a test liquid is known, it can be used to determine the surface energy of a solid by placing a droplet of the liquid on the surface. The contact angle ϴ can be measured between the surface and the side of the droplet. If ϴ is large, i.e. the droplet has a very round shape (see fig. 3 top left) this means wettability is low and therefore the substrate has a low surface energy. If the droplet is flat on the surface, i.e. ϴ is small (see fig. 3 top right) then the surface energy of the substrate is high. So-called Drop Shape Analysers (for example by https://www.kruss-scientific.com/ ) are a means for easy and reliable quantification of these parameters. They use two test liquids (for example water and diiodomethane) which, dosed into droplets, are placed onto a substrate to calculate its surface energy by accurately measuring the contact angle.
Application examples: Increasing surface energy
Substrates with low surface energies are challenging for processes like bonding, varnishing or printing since the respective medium, for example adhesives or varnishes, show poor wetting on the surface which decreases the process quality. By increasing the surface energy of the substrate material, be it a polymer, metal, glass, ceramic or textile, wetting can be enhanced which leads to a higher quality of the follow-up process. Relyon Plasma offers two different technologies for the enhancement of the surface energies of various materials: Pulsed Atmospheric Arc Technology (PAA®) and Piezoelectric Direct Discharge Technology (PDD®). Both are well established in the pre-treatment of surface for processes like printing, varnishing and adherence and will be introduced in the following using real application examples.
Treatment of Polyphenylene sulfide (PPS) with Plasmabrush® PB3 (PAA Technology®)
Polymers tend to have low surface energies which can lead to problems when gluing, varnishing or printing.
The surface energy of untreated polyphenylene sulfide (PPS) components is below 40 mN/m, as shown in fig. 1 through the contraction of the respective test ink which leads to the formation of droplets on the surface. With the help of the Drop Shape Analyser Kruss DSA 10, contact angles of the two test liquids water and diiodomethane (CH2I2) can be measured to determine the surface energy to be around 36 mN/m (see fig. 3). After plasma treatment with the Plasmabrush® PB3, the surface energy is increased to a value of 62 mN/m. By applying test inks, it can be confirmed that the surface energy now exceeds 60 mN/m since the respective test ink does not contract but forms a closed film on the surface, as seen in fig. 2. The plasma treatment significantly improves the preconditions for an effective follow-up process like gluing and guaranties reproducibility through well-defined process parameters.
Treatment of spring steel with Plasmabrush® PB3 (PAA Technology®)
The surface energy of the untreated spring steel component is determined by contact angle measurements to be roughly 42 mN/m (see fig. 4). These are not ideal conditions for processes like gluing. Clean metal surfaces usually have surface energies of a few thousand mN/m. Oxides and organic residue like lubricants and release agents used in the manufacturing process can lower the surface energy drastically. A rapid and inline-capable pretreatment with the atmospheric plasma of the Plasmabrush® PB3 can increase the surface energy in this case to around 66 mN/m (see fig. 4), a value usually more than sufficient for typical gluing processes. A set of parameters tailored to the process ensures the reproducibility of these results.
The application of test inks can help verify the plasma-induced enhancement of the surface energy and show the difference between treated and untreated surface area: In fig. 5 a test ink with a value of 66 mN/m was applied to the surface, wetting the plasma treated area perfectly while contracting to droplets on the untreated area.
Treatment of ePTFE with Piezobrush® PZ2 (PDD Technology®)
So-called Teflon tape or ePTFE is known for its ability to repel liquids. This is manifested in the very low surface energy of the material in this medical application example, which has been determined to be around 8 mN/m (see fig. 6). Low values like these are out of the range of typical test inks, which makes the contact angle measurement the significantly more conclusive method. For medical applications an enhancement of the surface energy of the ePTFE can be desirable. Treating the surface with the Piezobrush® PZ2 by injecting argon through its multigas nozzle can lead to a notable increase of the surface energy of up to 30 mN/m.
Conclusion
The surface energy is an important parameter for substrates that are to be treated in processes like gluing, varnishing or printing. It is essential for a surface’s wettability and is easily approximated with the help of test inks or accurately determined through contact angle measurements. If substrates are not wetted sufficiently by glues, varnishes, etc., the quality of the bond will suffer. Through a surface pre-treatment with atmospheric plasma the surface energy can be effectively and reproducibly increased: Relyon Plasma offers solutions suited for standard processes as well as individual applications.
Literature
Pocius, Alphonsus V. (2002). Adhesion and adhesives technology: An Introduction. Munich: Hanser.
Berg, John C. (1993). Wettability. New York: Marcel Dekker, Inc.