Integration example
Plasmabox: a compact solution based for plasma processes.
Thanks to our many years of experience in arc dynamics, fluid mechanics and power electronics, we have been able to develop an atmospheric plasma system that is unique in terms of power density and function. The development of this universally applicable plasma unit was focused on simple integration into industrial processes and the ability to communicate easily with higher-level control systems.
With this unit relyon plasma offers a compact solution on the newest state of the art, which can be modified according to the frame conditions. The basic structure of the plasma system consists of a plasmabrush PB3 plasma generator and a 19″ PS2000 high-voltage source in an IP54 housing made of robust metal that protects the internal components.
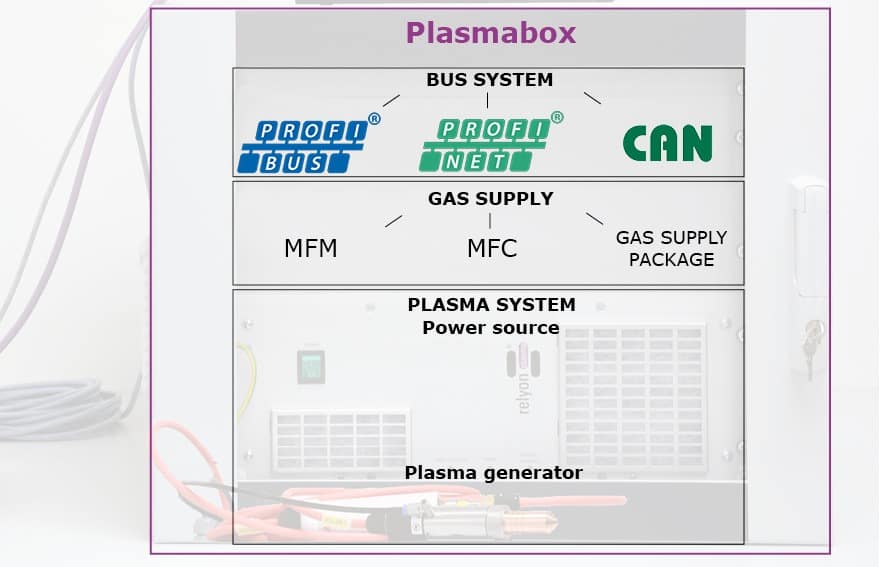
The existing housing offers the possibility to integrate a second high voltage source PS2000 and to operate two plasmabrush PB3 plasma generators. At the same time, it is equipped with two IP54 shields – one of which is equipped with an active fan to ensure good internal cooling. Flow control is performed by a maintenance unit in combination with a pressure valve.
It is also possible to interpose one (or two) flow sensor(s). The return data of the flow sensor (both above and below a threshold value as well as an analog voltage signal indicating the current flow rate) to the higher-level controller can be used to control both the process gas flow and the process gas consumption.
The Plasmabox can thus be easily integrated into an existing system and the plasma process can be started.
Application examples
Printing industry
Different types of pipes , cables, or other components have to be marked with information about material, production, date, batch, etc. Due to ever-changing regulations, the chemical composition of the ink has to be adapted for the printing process. In the course of such adjustments, chemical additives are removed from the inks which improve or have improved the adhesive properties of the inks. The surface energy of tubes the components to be printed can be increased by plasma pre-treatment. A higher surface energy simplifies the printing process. At the same time, the surface is heated slightly, which accelerates the drying process of the ink.
Varnishing
In almost all varnishing processes, the surface must be cleaned before the varnishing process. Examples of this are the automotive industry or customer-specific solutions for supplying the customer with a painted component in the customer’s corporate design. Not all surfaces have the same degree of cleanliness before the painting process. Touching the palm of the hand before applying the paint is sufficient to soil the surface to such an extent that the paint has poor adhesion. Where does this come from? The skin of every human being has a film of grease and water, which is transferred by contact with components. When transferred to the painting process, this means that the surface to be painted is contaminated with water and grease. Through plasma treatment with the PB3 system and simultaneous heat input, the aforementioned substances can be gently removed from the surface. At the same time another positive effect is achieved: the surface is activated. The plasma activation facilitates the subsequent adhesion process of the paint and the paint can unite better with the surface. This results in better adhesion and better quality.
Technical information
All connecting cables of the PS2000 high-voltage source are accessible from the outside. Integration into an emergency stop circuit of the higher-level control becomes a piece of cake. The 10-meere-long high-voltage cable allows the unit to be set up in a decentralized manner.
The CAN bus line allows easy integration into the higher-level control system – thanks to the CAN bus interface, the system can be integrated into almost any existing solution. Beckhoff, Siemens, Wago, and EATON are just a few examples. Various sensors or mass flow controllers use the same standard. All of the world’s most widely used industrial controllers provide the corresponding interface. Up to 127 devices can be controlled via a CAN node. The entire process control is managed via the CAN bus. This means that an accurate mass flow control for air and all process gas mixtures can be easily integrated into the system.
The entire system intelligence is implemented in the central control system. IXXAT/HMS offers robust interface modules for all typical automation solutions.
What’s the difference between ProfiBus and ProfiNet?
The Plasmabox can of course also contain two high voltage sources PS2000, a system expansion can be implemented very easily. Due to the modular system of the Relyon Plasma components, several systems can of course be coupled and several PS2000 high-voltage sources can be installed in a larger IP54-protected structure.
Are you looking for a more flexible solution?
Get in contact >>