Bonding properties of pressure-sensitive adhesives on white goods
At Adhesion’19 our colleague Corinna Little gave a lecture about the Bonding p
Abstract
The improvement of the adhesion of different pressure sensitive adhesives (PSA) on differently coated steel sheets by atmospheric pressure plasma jet (APPJ) treatment is investigated. Two types of APPJ have been applied: the pulsed atmospheric arc (PAA) based 700 W industrial device and 18 W piezoelectric direct discharge (PDD) based handheld plasma brush. The first is used for surface activation of coated steel sheets. The second – for treatment of the PSA layer on different adhesive tapes. The adhesion force is determined by a 90° peel strength test. It is more than doubled, if the PSA surface is treated as compared to an untreated PSA on a pre-treated substrate and partially cohesive failure is reached. Despite of an increase in surface energy after plasma treatment of the coated steel sheets, the adhesion force was only marginally increased and adhesive failure occurred with untreated PSA.
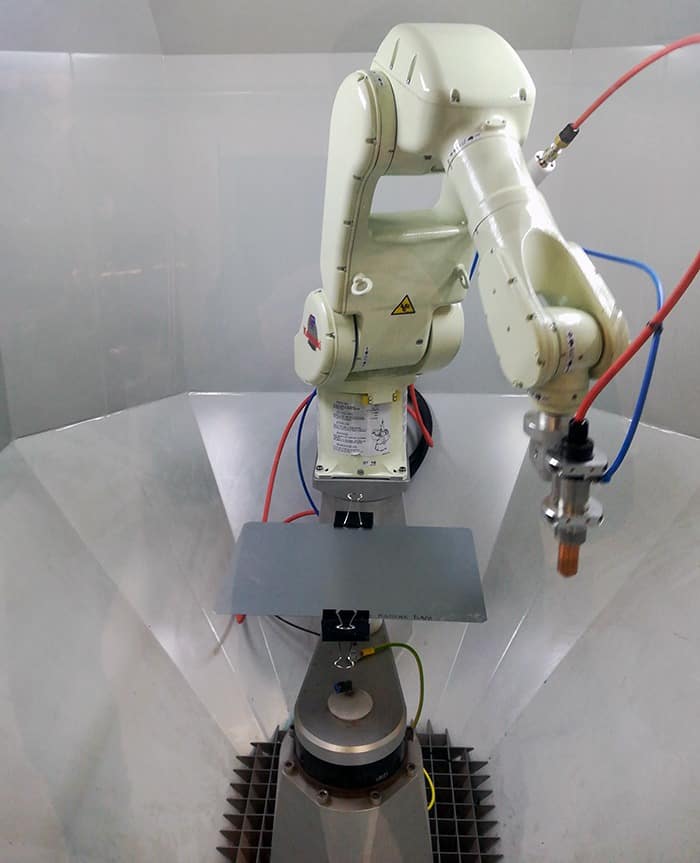
Introduction
Major appliances have taken on an important role in our lives and in our homes. Not only are they expected to be reliable and efficient, but also to be stylish and to canvass for its respective brand. Logos and embellishments are therefore applied to these products by many manufacturers, oftentimes by means of pressure-sensitive adhesives (PSA).1 However,
It is frequently used for improvement of the adhesion of PSA on different surfaces.3 Typically the material on which the PSA should adhere is plasma treated.4 But a strong improvement of adhesion on steel has been observed, when the PSA (PIB – poly(isobutylene)) and PBA: poly(butylacrylate) itself was pre-treated by oxygen plasma.5 The improvement of adhesion by pre-treatment by use of different types of plasma (APPJ,6 corona7, DBD8) for PSA based on natural and synthetic rubber, polyurethanes and acrylate is shown.9 The aim of this feasibility study is the evaluation of the influence of plasma treatment by use of different APPJ on the adhesion force of different PSA coated tapes on coated steel sheets.
Experimental methods and materials
For this study two plasma tools with extremely different properties have been used: On the one hand the Pulsed Atmospheric Arc (PAA) plasmabrush® PB3 system, consisting of the plasma generator PG3110 (shown with robot in Fig. 1) and powered from the high voltage pulse generator PS2000OEM and on the other hand the Piezoelectric Direct Discharge (PDD)11 handheld instrument piezobrush® PZ2 (see Fig. 2). The main specifications of both tools are compared in table 1.
Plasma tool | plasmabrush PB3 | piezobrush PZ2 |
Operation principle | PAA | PDD |
Nozzle used | A450 | Standard nozzle |
Plasma / Consumed power | 150 W / 700W | 8.3 W / 18 W |
Plasma plume temperature | Hundreds of °C | Close to room temperature |
Working gas | CDA | Ambient air |
Gas flow | 50 SLM | 10 SLM |
Operation frequency | 54 kHz | 50 kHz |
Nozzle distance | 10 mm | 2 mm |
Typical activation speed | 1 m/s | 1 cm/s |
The
A 6-axis robot Kawasaki RS05L (as shown in Fig. 1) has been used to move the PG31. The
Test preparation
The 30 cm long, 25 mm broad strips of PSA coated foils have been placed on the steel sheet surface and fixed by use of a contact pressure roller. The force applied by the roller was 19.62 N.
The steel sheets with two different coatings have been investigated: Multiface® and CC enamel varnish. Three different PSA coated foils are used: Astorplast, Ritrama and Tesa. For plasma treatment with PB3 the process parameter as summarized in table 1 are used.
The 90° peel strength test has been conducted 20 min after strip fixing by use of dynamometer Sauter Model FH500N.
Results and discussion
In the diagram in Fig.
The plasma treatment of the metal sheets alone is not enough to reach cohesive failure. All PSA strips show adhesive failure on both substrates.
Due to the treatment of PSA on the strips, the adhesion force for Tesa and Astorplast material on both metal sheet coatings has been significantly increased and cohesive failure could be observed. The residua of the PSA can be seen on the substrate shown in Fig. 5.
Conclusion
- This feasibility study shows, that a Pulsed Atmospheric Arc (PAA) plasma system operated with compressed dry air, can help prepare the CC
enamel coated steel surface bymaximising peel strengths of certain pressure-sensitive tapes by up to 68% compared to the untreated substrate. The results are comparable to a cleaning step with isopropanol. - Due to the high power density of the PB3
system a treatment speed of 1 m2/min can be demonstrated. - By treating the PSA coated side of the strips prior to bonding with a Piezoelectric Direct Discharge plasma, generated by
piezobrush PZ2, maximum peel strengths can be doubled compared to the untreated PSA strips on pre-treated coated steel substrates. Compared to the untreated PSA on the untreated substrates, the maximum peel strength is increased over sevenfold. - Two out of the three different types of
plasma treated PSA strips show partial cohesive failure on both the Multiface and the CCenamel coated steel substrates whereas the untreated samples all failed adhesively.
References
[1] Donatas Satas (1989). Handbook of[2] K.H. Becker, U.Kogelschatz, K.H. Schoenbach, and R.J. Barker (2005). Non-Equilibrium Air Plasmas at Atmospheric Pressure. Institute of Physics Publishing, London.
[3] Rory A. Wolf (2010). Plastic surface modification: Surface treatment and Adhesion, Hanser Publications, Cincinnati, pp. 23-32, ISBN-13: 978-1-56990-447-3.
[4] A. Baldan (2004). Adhesively-bonded joints and repairs in metallic alloys, polymers and composite materials: Adhesives, adhesion theories and surface pretreatment, Journal of Materials Science 39, pp. 1 – 49.
[5] M. Kawabe, S. Tasaka and N. Inagaki (2000). Effects of surface modification by oxygen plasma on peel adhesion of pressure-sensitive adhesive tapes, J. of Appl. Polymer Science 78, pp. 1392-1401.
[6] J. Winter, R. Brandenburg
[7] J.-S. Chang, A. Lawless, and T. Yamamoto (1991). Corona Discharge Processes, IEEE Transactions on Plasma Science 19 (6), pp. 1152 – 1166.
[8] U. Kogelschatz (2003). Dielectric-barrier Discharge: Their History, Discharge Physics, and Industrial Applications, Plasma Chemistry and Plasma Processing 23(1), pp. 1-45.
[9] A.Koops, M. Kupsky, K. Keite-Telgenbüscher, S. Zöllner and T. Schubert (2017). Method for increasing the adhesion between the first surface of a first web-type material and
[10] Relyon Plasma GmbH: Operating instructions Plasma generator PG31. http://www.relyon-plasma.com/wp-content/uploads/2016/05/plasma-generator- PG31- manual-EN_F0298601.pdf, (2014), [Online; accessed 12-April-2019].
[11] Relyon Plasma GmbH. Operating instructions for
[12] Korzec, D.; Burger, D.; Nettesheim, S.: Plasmaaktivierung von Rolle
Here you can download the full article: Bonding properties of pressure-sensitive adhesives on white goods